Introduction To Blocking A Single Wide Mobile Home.
Table of Contents
I have chosen to write about blocking a single wide home for clarity. Blocking a multi-section home is the same process in principle if we ignore the need to move one section towards the other. I have chosen to describe the method using manual tools and concrete blocks and ABS pads.
Before you can go about blocking a home there are a number of important considerations to bear in mind. I have tried to explain these further in detail below but if you want to go straight to the actual construction process continue reading.
The12 Steps
- Site preparation
- Position the home
- Secure the hitch
- Jack up One Side
- Lay out materials
- Cut in the base pads
- Install a vapor barrier
- Water level the 1st beam
- Raise the jack
- Level the piers
- Lower the beam onto piers
- Tighten wedges
How To Block A Single Wide Mobile Home – Full Instructions.
Step 1 – Site Preparation.
Get permission to install the home and permits if necessary.
Ensure that the mobile home foundation pad/fill dirt is deep enough and wide enough to support the weight of the home for several years to come. Make sure that the pad slopes away from the house and prevents running water from accumulating under the home.
Post your permit and blocking plan in plain sight.
Step 2 – Position The Home On The Foundation Pad.
Using a tractor or tug, pull the mobile home onto the foundation pad. Pulling rather than pushing will prevent the home from digging into the pad too much. Make sure that the home it is lined up exactly the way that you want it to be for the foreseeable future.
If the ground is soft, use homemade mats made from plywood to keep the tires on the top of the ground.
Repair any tire marks or ruts back to their original condition with a rake and shovel.
Step 3 – Secure The Hitch.
Ensure that the hitch is stable and supported on sufficient wood with a metal plate under the stinger. There could be several tons of weight resting on the hitch. The hitch will tilt from side to side as you raise and lower the jack but it still needs to be on a secure footing.
Raise the hitch by turning the handle or stinger. The I beams at the hitch end of the home need to be slightly higher than the final leveled elevation.
The tires and the hitch will prevent the home from falling completely to the ground in the event of an accident with a jack whilst lifting the home.
Never remove the hitch or axles until the home is completely set down onto the new block foundation.
Step 4 – Set Up The 1st Jack.
Set up a 12-ton jack behind the axles on one side of the home only.
Do not raise the home yet, just get it prepared and ready for now to use in step number 9.
Step 5 – Place Materials Next To Piers.
According to your blocking plan, mark the location of all of the piers on one side of the home. Use a tape measure and a pencil to mark the bottom row of lap siding.
Place a complete set of materials for building a pier next to each pier location. This will ensure that you will not have to keep getting up and walking to the supplies and back before you can stack each pier.
- 2 – concrete cell blocks
- 1 – solid cap block
- 1 – 2″x 8″x 16″ boards pressure treated
- 1 – 1″x 8″x 16″ boards pressure treated
- 2 – wedges pressure treated
Keep all of the materials in separate piles adjacent to each pier location, neat, tidy and within easy reach while you are working.
Step 6 – Cut In The Base Pads.
You will now be working under the home at each marked location.
Using the shovel remove any grass before laying down one of the foundation pads. Scrape back more grass than needed for easier adjustment. Level each pad accurately with the torpedo level, making sure to center the glass bubble in both directions.
Continue to level all of the base pads around the home until they are all completed.
Note: The tires will be in the way of maybe 2 pads on each side. Leave these materials out for now.
Step 7 – Install The Vapor Barrier.
Take the roll of plastic to the hitch end of the home. Remove the wrapping and place the roll on the ground between the I beams. Lay the roll so that it will open up as it is rolled from one end of the home to the other. Cut off the end level with the end wall of the home.
Stretch the plastic over the foundation pads and place the 2 cell blocks on top of the plastic to hold it in place. If you are alone work on one side at a time from end to end. However, if you have a helper it is better to work side to side moving down the length of the mobile home.
Leave the plastic sheet behind the tires, we will deal with this issue later.
Step 8 – Water Level The Beam.
Set up the water level. Place the level at the end of the home out of the way of any activity. Place the bottle on blocks and wood raising the level of the water in the container to around 20 inches from the ground.
Using the tape measure and the loose end of the level, walk around the home and check the height at various locations. The objective is to make sure that you will not be too low at any particular point around the home. For example, if the level is showing around 20 inches from the ground to the bottom of the beam in 4 corners but only 15 inches in the center. In this case, you may need to raise the overall height of the water jug to get sufficient clearance.
Check all four corners and the middle of the home to get a good idea.
Step 9 -Raise The Jack.
Using the jack previously put in place raise one side of the home so that the beam is 1-2 inches higher than the water level. Click here for more details.
Step 10 – Leveling The Piers.
Build the support piers working down the home from the hitch end towards the rear. Using the water level, set the height of each pier to the height of the bubble visible at the end of the tube. Make up the difference between the cell blocks and the level using cap blocks, wood and wedges as needed.
If the beam is not high enough, raise either the jack or the hitch by turning the handle. Continue to level down one side until all of the piers have been leveled apart from the two behind the axle.
Step 11 – Lower The Leveled Beam Onto Piers.
Using the jack handle, carefully release the jack slowly and allow the beam to come down onto the pre-leveled piers.
Follow steps 9 through 11 on the other side of the home. At the end of this step, the majority of both I beams will be resting on the adjacent piers. Finally, turn the hitch stinger anticlockwise to release the pressure and allow the front of the house to come to rest on the piers.
Step 12 – Tighten The Wedges.
Go around the completed home and check the position of the wedges on top of each pier. Make any minor adjustments to the wood and drive the wedges tight with a hammer.
You have now successfully blocked a single wide or the 1st half of a double wide mobile home.
What Tools Do I Need To Set A Single Wide Home?
- Sharp square head shovel
- Garden rake
- Tape Measure
- Pencil
- 12-ton bottle jack and jack handle
- Claw hammer
- One 7/8″, 13/16″, 15/16″ sockets
- Two 1/2″ ratchet drivers or impact drivers
- 13/16″ and 15/16″ wrenches
- Torpedo level
- Water level complete
- Small battery headlight
- Pair of gloves
What Materials Do I Need To Block A Single wide Mobile Home?
- Plastic Sheeting
- Cell Blocks
- Solid Cap Blocks
- Wooden Shims
- Wooden Wedges
- Concrete or ABS base pads
How Far Apart Should Mobile Home Piers Be?
Mobile home support piers and the I beam rails beneath the home combine to create a pier and beam foundation. Usually, these piers are built by loosely stacking cell blocks on a base pad and capped with a concrete block, pressure treated timber or a combination of both. Each support pier carries a portion of the total weight of the home. The pier transfer the load down to the ground.
Mobile Home Pier Spacing.
The distance between the piers on a mobile home is determined by calculating the load-bearing capacity of the dirt pad, the weight of the home per foot of I beam and the capacity of the base pads in square inches.
However, as a rough guide, 6 feet on center is a good average starting point.
Mobile Home Pier Spacing.
Generally speaking the more piers under a mobile home the better. For instance, each extra 16″x 16″ pier pad increases the load-bearing capacity of the foundation system by 256 square inches or 1.77 square feet. What is even better is larger pier pads installed closer together.
Use The Chart From The Home Manufacturer.
To determine the distance on a new mobile home refer to the charts in the manufacturers’ installation manual which will accompany the home. The manual and sometimes blocking diagrams will be supplied by the manufacturer and placed in the homeowners’ welcome packet, usually this can be found in a kitchen drawer.
Chart From Hud Or State Code.
For used homes, it is recommended that you use the chart from the Department of Housing and Urban Development (HUD) website, which looks like this:
What Is The Typical Maximum Height Of A Single Block Pier?
Single stack block piers have a maximum recommended height of 36 inches on the main beam and 24 inches on any corner of the home. Above these heights, the block piers need to be double stacked up to a maximum height of 67 inches and capped with a solid 4-inch block.
Beyond 67 inches it is advised and required in some states to use specially engineered plans which may call for poured concrete blocks and the inclusion of rebar for strengthening.
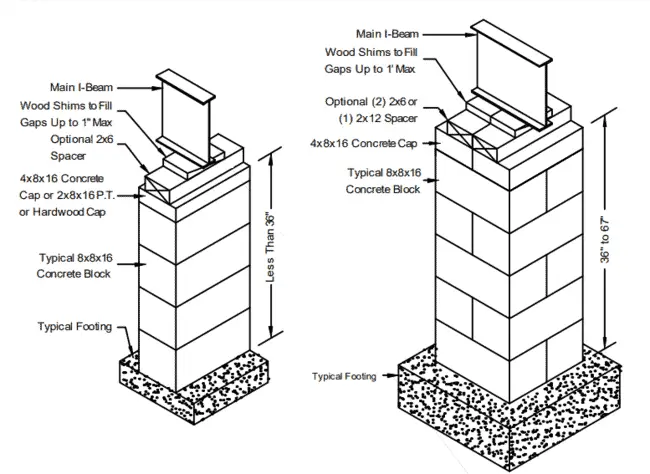
Septic Tank Drain Field Height.
In order to prevent sewage from being washed around during wet conditions, many septic tank drain fields are installed at higher elevations than normal. This minimum height is set by the health department using Fema Flood Regulations.
To get sufficient “drop” on the sewer waste pipes, homes have to be set higher than they would have been normally. The plumbing pipes under the home are connected together in the space below the I beams and they need sufficient height to flow by means of gravity to the system.
FEMA Flood Zones And The 100 Year Flood Plan.
The Federal Emergency Management Agency (FEMA) has mapped out the whole of the United States. Fema has assigned a flood zone designation for each region, for example, flood zone A, flood zone Y. Flood zones designations depend upon the percentage chances of a catastrophic flood occurring in the next 100 years.
These flood zones are nationwide and all states must comply with the rules. Some flood zones require mobile home door thresholds to be 56 inches above the highest adjacent grade or higher.
What Is The Lowest Height For A Mobile Home Set?
I would not set a home below 20 inches to the I beam unless it is on a slope. Then 75% should be over 18 inches.
20 to 30 years ago people that bought a mobile home wanted it to look like a conventional home. They tried all kinds of ways to achieve this including digging a 24-inch deep hole in which to place the home. This was called a pit set and usually managed to put the front door threshold down at ground level. Another method to keep the home low was to set the home on a 2-inch concrete base pad. These methods are no longer used.
Today’s mobile homes need to have at least 18 inches of free space below the I beams. It is better to have more. This space allows for plumbing pipes and HVAC system ductwork. R8 ducting has a 16-18 inch diameter and needs to be 4 inches off of the ground.
Foundation Pads For Mobile Homes.
The foundation pad is the footer of the support pier which sits on the top of the ground beneath the stacked block.
Concrete Foundation Pads.
Concrete pads measuring 16″ x 16″ x 4″, and weighing around 60 pounds have been used for the base pads of mobile home piers for around 50 years. They are heavy and very awkward to move around under a home They are also not easy to get level in a reasonable length of time.
I don’t use them and I don’t suggest that you do either unless of course, you have a big stack of them lying around. The new abs pads are superior for a number of reasons.
ABS Plastic Pier Pads.
These pads are light and easy to use. They are made of 1 inch thick ABS plastic which is engineered with ribs to prevent the pads from bending and deflecting under a load. They come in a number of useful sizes each one able to support a specific load in pounds per square inch (PSI).
When it comes to the load-bearing capacity of mobile home support piers, the size of the pads (ie. Footprint) matters more than anything else.
Do I Need A Plastic Vapor Barrier Under The Home?
In Florida, we are required to install a 6mm thick polyethylene vapor barrier on the ground under a new mobile home. This is to prevent water, in the form of vapor, from damaging the structure of the home. However, on used homes, the plastic barrier is not required.
The plastic goes on the top of the ground and covers the base pads. It is held in place by stacking the block on top of the pads and by stretching it over the anchor heads. On balance I would install a vapor barrier on my own mobile home whether it was required or not.
This plastic is readily available at Lowes and Home Depot in 100 ft rolls.
Mobile Home Blocking Diagram.
Below is a typical mobile home diagram showing the size of the pier pads and the distances between each pier.
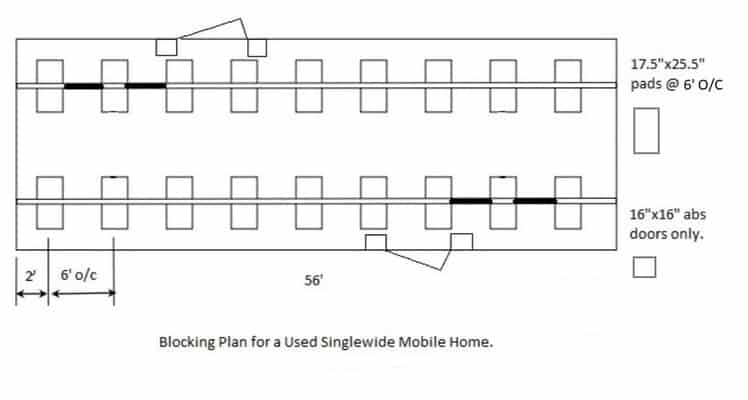
How Do You Jack Up A Mobile Home?
Secure the hitch and stinger on layers of wood with a metal plate.
Find a clear flat area beneath one of the I beams, ideally behind the axles and tires. Drop a stone from the beam to the ground to find the center. Place a minimum of two interlocking rows of 2″ x 8″ timber centered under the beam.
Place a 12-ton bottle jack on top of the wood. Extend the screw until it touches the underside of the beam. Alternatively, you can add more wood to close the gap.
Tighten up the hydraulic screw, insert the jack handle and slowly pump the handle up and down until the required height is reached. Watch the home as it rises and check that the jack is remaining vertical and centered.
How Long Does It Take To Set Up A Single Wide Mobile Home?
My crew of two men can set a single wide mobile home, with a water level, on concrete block piers, with the axles tires and hitch removed, in less than 2 hours.
Anchoring and tying down the home will take another two hours to complete. For a total of 4 hours. This installation would be completely finished and to code.
With a Translift and an Eager Beaver anchor driver, the installation time should be much faster.
Also Read: What Will It Cost To Level My Mobile Home – Relevel Costs
Mobile Home Perimeter Piers.
Some mobile homes will require perimeter piers to be installed usually between 5-8 ft on center around the perimeter of the home. Perimeter piers help to support the weight of the home along the walls.
These homes are usually 16ft or 18ft wide where the beams are a greater distance from the edge of the home and the walls have conventional drywall panels installed.
Some older homes where the I beams are less than 82 inches apart also require these extra piers.
Conclusions.
Not all states in the USA allow homeowners to install their own mobile home.
This lengthy article describes the process to follow in order to block a mobile home. Although the information is correct, this job is definitely not for everyone to attempt. If you need help with setting your home please give us a call now on (863) 808-2200 to arrange a meeting to discuss your needs.
You can also get in touch with us by using the contact page.